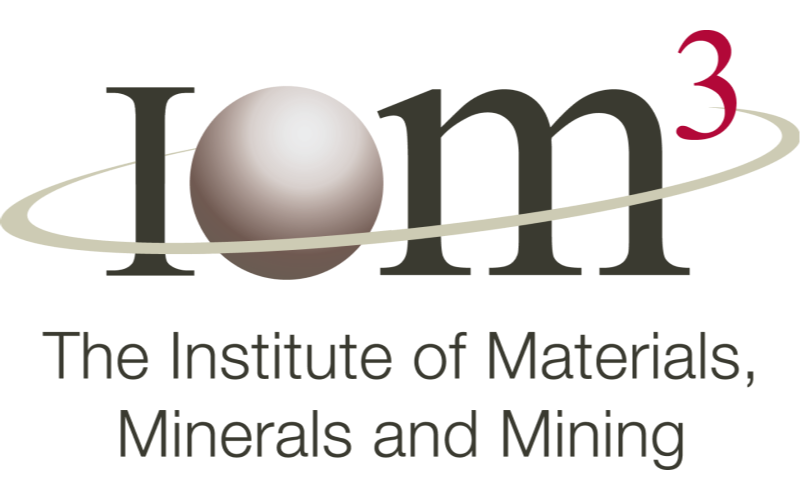
Materials World magazine, 29 Sep 2020
While developing wire arc additive manufacturing, researchers in Russia have discovered a surprising improvement in aluminium’s ductility. Idha Valeur catches up with them.
Enhanced elongation in aluminium to 41% is being reported by scientists in Russia. This is three times higher than the standard 12% and means the material should be more durable under the same workloads, says the team at Peter the Great St. Petersburg Polytechnic University.
Originally focused on developing high-performance, wire arc, additive manufacturing (WAAM) technology for aluminium parts, they were surprised when the research led to improved ductility in the metal. Oleg Panchenko, Head of the Laboratory of Lightweight Materials and Structures at the University, explains, ‘We developed special arc voltage and current waveforms for WAAM to increase process productivity. With use of it, aluminium bricks and walls were 3D printed. And standard samples for tensile tests were cut from those walls and bricks.
![]() |
Credit: Peter the Great St.Petersburg Polytechnic University |
‘During [these] tests we found that specimens behave specifically, almost no necking of specimens occurred [and] elongation was higher than anything that we saw before. Then we did some experiments to study the mechanism of such ductile behaviour and found that it is supported by two factors: grain size and pores collapse.
‘Grains became elongated and pores became smaller. Dislocations were able to move more freely through elongated grains. [The pores’ size] made its collapse (closure) possible during loading.’
The importance of this discovery, he asserts, is two-pronged. ‘Scientific importance is in the mechanism that supports such ductile behaviour of the material, which may be transferred to alloys based on other metals (magnesium, iron, nickel, etc.).’ He adds that there is a correlation between ductility and fatigue performance of material, but this needs further investigation.
He continues, ‘[Of] practical importance is the fact that obtained properties are not in the range of 1-5% higher but about three times. And that will lead to change [in] parts design.’ The benefit of such a ductile aluminium means that components could be designed to require less material and lead to reductions in weight.
The team foresees application in transport such as aerospace, automotive and shipbuilding. Panchenko explains that weight reduction will be especially beneficial for the automotive industry as it will lead to decreased energy consumption and carbon emissions.
As no special laboratory equipment was used to enhance aluminium’s ductility, Panchenko insists it is 100% repeatable in any industrial environment. However, he highlights that it is essential that parts are 3D printed and tested, as the Russian team only worked on ‘standard specimens’ and not parts or structures.
In the meantime, the team is investigating the mechanisms behind the ductile property. ‘It is well understood and explained by us in the paper that there is pores collapse that leads to…increase in ductility. But what is the mechanism of such collapse?’ Panchenko asks.
He adds that fatigue behaviour is of interest, ‘since there is some data in literature that shows improvement of fatigue properties for metallic materials with increased ductility’.
Source: https://www.iom3.org/