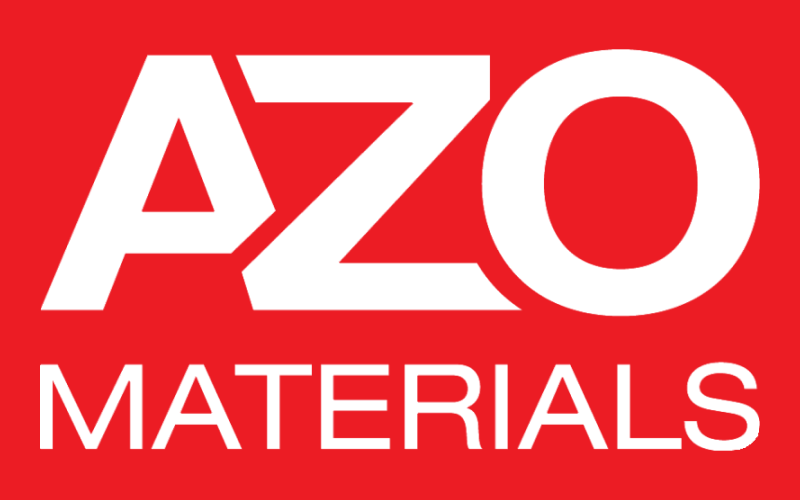
AZoM talks to Dr. Oleg Panchenko about his work with the Lightweight Materials and Structures Laboratory in SPbPU, and their project that looks to create a new lightweight footbridge employing a novel aluminum alloy and friction stir welding technique.
Please could you introduce yourself and your role within Peter the Great St Petersburg University (SPbPU)?
My name is Oleg Panchenko; I am Assistant Professor at the Institute of Mechanical Engineering, Materials and Transport, Head of Lightweight Materials and Structures Laboratory, and CEO of the "Kawasaki-Polytech" technological center at the Peter the Great St. Petersburg Polytechnic University (SPbPU). In 2012, I completed my Ph.D.
Currently, I work in the materials science field, but originally I came from welding, so it is a very important topic for me. My great passion in science and most of my current projects are in the Wire Arc Additive Manufacturing field. Industrial robot application development is also a part of my professional duties. The trend now is in machine vision and learning, so part of my job is to use this.
Since 2016, I have been the Russian Federation delegate at the International Institute of Welding. As of 2021, I became a Russian representative expert in ISO TC44, and an expert of the Russian technical committee 364 (National standardization in welding). I am the author of 30 scientific papers (according to Scopus database), and 15 patents.
Could you tell us a bit about the Lightweight Materials and Structures Laboratory in SPbPU?
The lightweight materials and structures laboratory is a part of the scientific division of the Institute of Machinery, Materials, and Transport at SPbPU. The Laboratory was founded in 2014 with the financial support of the Ministry of Education and Science of the Russian Federation, within the framework of mega grant projects.
The philosophical approach of the lab is to develop new materials and technologies until they can be implemented into new structures. For that, we have a multidisciplinary team that consists of 20 employees: material scientists, welding engineers, condense material physicists, etc.
We have been developing different types of composites on the basis of the aluminum matrix to increase the stiffness and mechanical properties of structures. We are developing technologies now for joining these.
We offer new specialized materials protected by patents and methods for the production of new structures for the aerospace, automotive, and shipbuilding industries. The laboratory also serves as a scientific and auxiliary base for high-quality training of a new generation of engineers and young researchers in the field of technology development.
One of the examples of our work, and the subject of this interview, is the development of a new aluminum alloy friction stir welding technology for bridge construction.
Oleg Panchenko in the Lightweight Materials and Structures Laboratory in SPbPU. Image Credit: Oleg Panchenko
What is friction stir welding?
Friction stir welding is the process of joining metallic materials in a solid state. Due to the rotation of a special toll inside the weld joint, heat is generated and metal is plasticized on the edges of the joint. Rotation of the tool mixes the metal of one edge with another and forms solid material.
This welding method is especially economically effective for aluminum alloys due to high welding speed; it also provides high mechanical properties of the products. This method is very efficient and therefore cost-effective.
How is friction stir welding employed to improve the construction of bridges?
The performance of friction stir welding is superior to other welding techniques for aluminum. In the process of structure manufacturing such as bridges, in particular, which have long welded seams, the financial efficiency of the technology importance is very high, i.e. we spend less time to weld the elements and, as a result, we get economic benefits. This happens, for example, due to the fact that we can weld parts of a bridge with a large thickness of 16-25 mm not in 10 weld passes, as in the case of electric arc welding, but in 2. Also, the product has high mechanical properties; the strength of the joint itself is not lower than the initial strength of the material used for production.
In addition, friction stir welding is a green technology because there is no evaporation of material or light emission.
Welding robot inside the 'prism'. Image Credit: Oleg Panchenko
Your lab has utilized this technology create a model for a new pedestrian bridge. Please could you outline for us the design of the bridge model and why it is significant?
Our scientific group was the first in Russia to develop a friction stir welding technology of a new aluminum alloy for a lightweight pedestrian bridge.
This aluminum pedestrian bridge will be located in the town Bor in the Nizhny Novgorod region (Russian Federation) as a part of the recreation zone at the beach of the Volga river.
This will be the tenth aluminum pedestrian bridge in Russia, but previous ones were made as highway pedestrian bridges, and our bridge also differs from predecessors as it uses a new alloy and friction stir welding technology.
We have been working in collaboration with the SGR aluminum structure plant in St. Petersburg. The project was supervised by the Aluminum Association of Russia. The engineers of the laboratory joined 20 parts that were 8 meters long and 16 mm thick.
It is more economically beneficial to weld thick aluminum parts in this way because arc welding uses a number of additional manipulations (for example, arc welding is carried out in several passes to fill the entire thickness of the seam with the filler wire).
3D render of the bridge project. Image Credit: Alumforum
For the construction of the bridge, a new aluminum-magnesium alloy was used. Who created this and what are its properties?
In Russia, 1565 is the name of this alloy; it is a new development that has just recently become available for widespread use. It was developed by Russian scientists led by Dr. Alexander Drits, who is not part of the Polytechnic University. However, our research team were the ones to test the weldability of this alloy in 2016. In 2021, we applied our knowledge to create a pedestrian bridge.
The properties of this alloy are a little bit higher than of the 5056 series, for example, and the main alloying elements are aluminum and magnesium. Its production is easier, which helps to reduce its cost. Also, the alloying characteristics make this alloy more durable. In Russia, this is the 1565 alloy, but in the international classification, it is the 5000-series.
How is this alloy suited to use in bridges?
In order to provide high-quality joints, we preliminarily carried out tests on the weldability of this aluminum and developed the welding technology using a friction stir welding machine.
The new high-strength aluminum alloy successfully competes with the structural steel in terms of stiffness and corrosion resistance; also, the aluminum structure will be much lighter than the steel ones, so bridge construction will be easier and cheaper.
How will bridges made with this new material and method compare in strength and durability to more traditional bridges?
Although currently there are not many aluminum bridges both in Russia and the rest of the world, they have important advantages over steel ones.
For example, the material properties of steel bridges change with temperature; when temperatures lower, the metal becomes more brittle. This is not the case with aluminum.
In addition, compared to steel, aluminum bridges can be installed quickly and easily (no special heavy cranes and equipment are required). This speeds up the construction process.
Further, aluminum has a high corrosion resistance compared to steel, and the structure of the aluminum bridge can be as stiff as steel ones with less weight, due to the material's strength-to-weight ratio. Aluminum has one of the best ratios in this regard; this is why it is used for aircraft fuselage manufacturing.
In my opinion, aluminum bridge construction will be actively developed in the future.
Is this process easily reproducible and is it cost-effective?
Welding is a completely reproducible process. The cost-efficiency of aluminum bridges is still to be discussed, as there are too many factors that can affect construction expenses. However, it should be considered that the ease of installation reduces the cost.
How will this bridge be unique compared to other aluminum bridges already constructed?
The main unique feature of this bridge is that it is not just a pedestrian bridge that simply serves as a crossing; it is a design solution for citizens’ recreation, which improves the urban environment.
Source: AZO MATERIALS